1,4 Butanediol
1,4 Butanediol
GROUP SECTION
LOCATION
China was selected as the country to produce BDO due to the market, the next stage was to determine an exact location in China to base the plant. The USDA foreign agricultural service report states that China’s sugar production in marketing year 2018/19 is forecast to rise for the third straight year by 600,000 tons to 10.8 million tons and in addition to this, imports are set to fall again.
With regards to sugar cane, 2018/19 production is forecast at 9.4 million tons, up 300,000 tons from the revised 2017/18 estimate. This can be attributed to price supports for farmers that have been recently introduced, encouraging growth and expansion. It was decided that the plant will be located in Guangxi, an autonomous region in South Central China, bordering Vietnam. It contributes to 65% of sugar production in China and with good transport links and growth expected, is an ideal location for our plant.
With the plant being located in Guangxi, and a forecasted 9.4 million tons of sugarcane being produced in 2018/19, an estimated 855,400 tons of sugarcane bagasse available to us to use as a feedstock.
INTRODUCTION
Product
A range of potential products that were considered to be produced. 1,4-butanediol (BDO) was selected as the best option due to its market size, potential growth and large range of applications. After the final product had been chosen as BDO, a thorough market analysis was carried out to find the best place to locate the plant. China was selected as the best country in which to operate as it exhibits the highest BDO production rates of any country accounting for more than half of global production which shows that it is a suitable climate in which to operate. In addition, China has the highest BDO consumption of any individual market accounting for 41% of total global BDO consumption. The next largest consumer is the rest of Asia at a significantly lower 22% share and by operating in Southern China this gives easy access to many of the most lucrative markets in this area such as Vietnam and Indonesia. The Asian market is also considered to be reliable moving into the future with estimated compound annual growth rates as high as 8.5% in the years leading up to 2025.
Feedstock
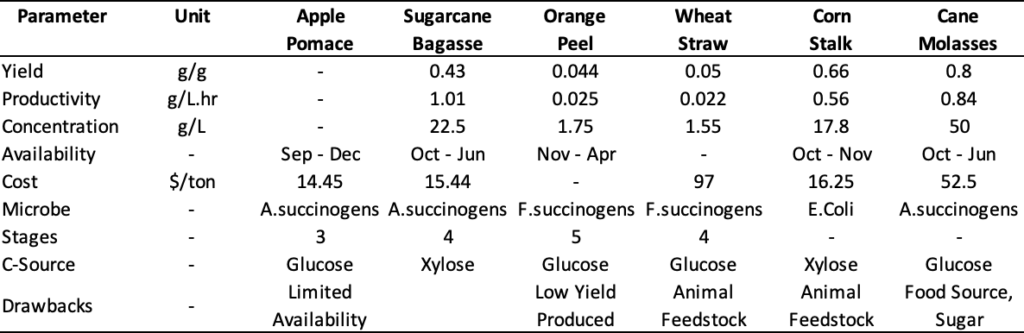
Using this information, a decision matrix was composed (see appendix A) from which a feedstock was chosen. Due to the vast range of qualities that SCB possesses, coupled with the fact that it is abundant in China, the location of our plant, it was decided that SCB would be used as the feedstock for the process.
Annual global production of sugarcane is 1.6 billion tonnes, from which 279 million tonnes of biomass residues are produced[9]. It is a fibrous residue of sugar cane stalks, left over after the crushing and extraction of the juice from sugarcane. SCB is composed of a variety of components rich in quantity, like cellulose, hemicellulose, lignin, ash and small amounts of extractives[10].
280kg of SCB is produced per tonne of sugar cane. From this, 50% of SCB is currently used for energy generation on the plant and the rest is stockpiled[9, 10]. The excess 50% is what would be available to us as a biomass feedstock.
Process
The process can be split into two sections, A and B. Both sections have individual PFDs. Section A represents the conversion of the feedstock, SCB, to succinic acid via fermentation and separation. Section B is the hydrogenation and distillation of the succinic acid to produce the desired BDO.
Section A
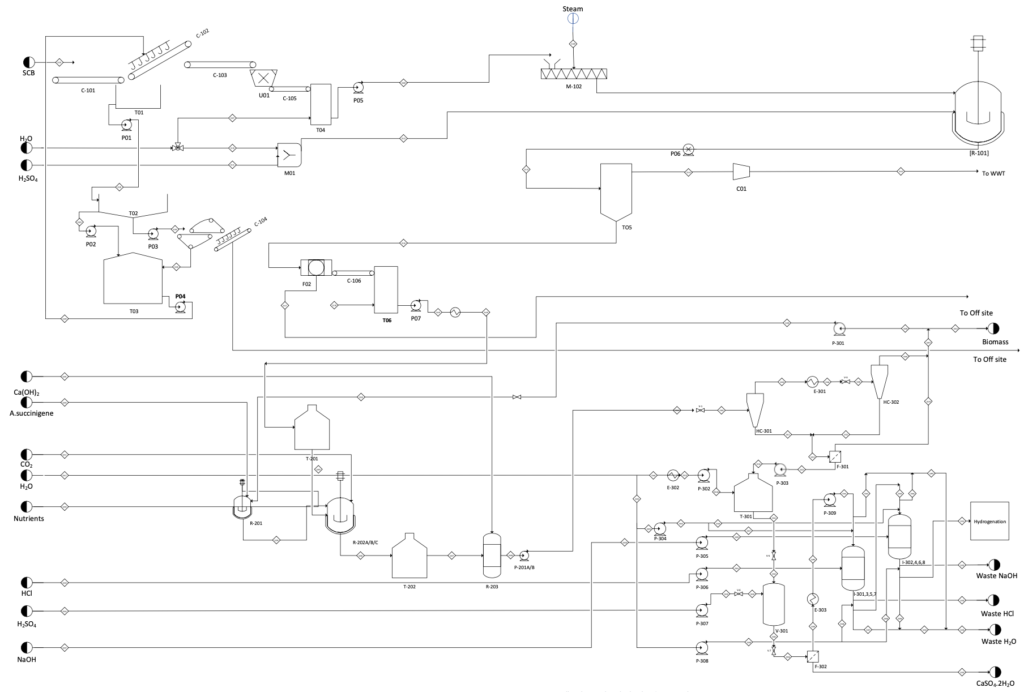
Section A: Pre-treatment to Succinic Acid Process Flow Diagram
Pre-Treatment
The aim of this process was to convert the SCB to fermentable sugars via steam and dilute acid hydrolysis. The SCB is received and some is sent to on-site storage while the rest is sent directly to the conveyors.
The SCB treated on the wash conveyor [C-102]. Here it is sprayed with water on a 45o incline, where a chain with metal teeth is used to pull the SCB up the incline. This washes any dirt or grit off the product and allows the water to drain from the SCB. By washing the bagasse prior to shredding it removes the ash and minimizes the amount of moisture absorbed by the product.
The washed SCB is discharged onto a conveyor [C-103] where it then reaches the miller [U01], which reduces the bagasse to the adequate size (30 − 50𝜇𝑚) for pre-treatment. A smaller particle size provides a greater sugar yield and is supported in several pieces of research. There is a recycle loop present using a clarifier [T02] to clean the water used to wash the bagasse and re-use it. Any underflow from the clarifier is primarily topsoil and sugarcane residue and is disposed of via land application to nearby fields.
The washed and shredded SCB is pumped to the pre-treatment stage and first steamed with low pressure steam in the screw conveyor [M-102] to 100oC. This is to break down the structure of the lignocellulosic biomass and make it susceptible to acid hydrolysis.
After the bagasse has been steamed it is fed into the reactor [R-101] for the hydrolysis of the SCB. Dilute sulfuric acid (1%) is added to the reactor to facilitate this. The total bagasse mixture now constitutes 30% insoluble solids.
The effluent from the pre-treatment reactor is flash cooled to 1 atm in [T05]. This is done to remove the unwanted by-products from the reaction. The top stream vapour is condensed in [C01] before being sent to wastewater treatment. The hydrolysate bottom stream slurry is sent to a pressure belt filter press to separate the solids and liquids. This is done to reduce the toxicity and remove potential inhibitors from the resulting processes. This filter was chosen as it provided the best recovery of solids and insoluble materials with minimal water. The cake is conveyed off the filter onto a transport conveyor and into the slurry tank [T06] where it is mixed with water to the desired solid/liquid ratio ready for the fermentation stages. Finally, stream [S-119] is heated to 37°C ready for fermentation.
Fermentation
Actinobacillus succinogenes culture is prepared. The bacterium is provided with nutrients consisting of NaCl, MgCl2.6H2O, CaCl2.2H2O, NaCOOH, Na2S.9H2O to enable faster growth. Since the bacterium is sensitive to temperature and pressure, the seed fermenter is maintained at 1 atm and 37 oC. A recycle stream containing nutrients and water is sent from the separation process to re-use available resources. The liquid phase stream from the seed fermenter now proceeds to go into the fermenter.
Xylose from the pre-treatment unit is sent to the Storage vessel (T-201) which is in the liquid phase. Later, sent to the fermenter (R-202A/B/C) as the batch is started. CO2 and the prepared bacteria culture from the seed fermenter (R-201) are added to the fermenter. All the feed entering from the previous vessels are at the required fermenter temperature and pressure.
Fermenter (R-202) carries a batch anaerobic fermentation for a duration of 48 hrs through a series of reactions to ultimately produce the desired intermediate succinic acid C4H6O4 represented by Equation – 4; whereas Equation – 1 to 3 shows the intermediary products such as Acetic, formic and pyruvic acid. This reaction is limited to a pH of 6.8 and a temperature of 37 °C, which is suitable for the bacteria to continue the chemical process. This liquid stream containing succinic acid and other reaction by-products are then sent to the storage vessel (T-202).
Reactions:
C5H10O5 (Xyl) + 5/3 H2O → 5/3 C2H4O2 (A.A) +5/3 CO2 Equation 1
C5H10O5 (Xyl) + 5/3 H2O → 5/3 C2H4O2 (A.A) +5/3 CH2O2 (F.A.) Equation 2
C5H10O5 (Xyl) → 5/3 C3H4O3 (Pyr) Equation 3
C5H10O5 (Xyl) + 5/3 CO2 → 5/3 C4H6O4 (SA) +5/3 H2O Equation 4
The content from T-202 are fed to the reactor (R-203) where it is combined with Ca(OH)2. It serves the purpose of precipitating calcium succinate (CaC4H4O4) as shown in Equation – 5. The calcium succinate is then sent to the downstream processing for separation.
C4H6O4 + Ca(OH)2 → CaC4H4O4 (Ca.SA) + 2H2O Equation 5
The reaction conversion numbers have been estimated after analysing literature on similar scale production of succinic acid as shown in Table

Separation
Fermentation broth consisting of calcium succinate, nutrients, water, cells etc are sent to a series of hydrocyclones (HC-301,302) to isolate calcium succinate along with water from the other components. The underflow of both the hydrocyclones is fed to a filtration unit (F- 301) to reduce water quantity.
The water along with the nutrients that are separated is recycled back into the seed fermenter tank (R-202). Freshwater (80oC) is then injected along with calcium succinate into a tank (T- 301). Calcium succinate (CaC4H4O4) which is now mixed with hot water is sent to an acidification vessel (V-301) where sulfuric acid (H2SO4) reacts with calcium succinate to form free succinic acid (C4H6O4) along with gypsum (CaSO4.2H2O), which precipitates out of the mixture represented by the Equation 6. The gypsum is filtered off (F-302) and discarded off to landfills.
CaC4H4O4 + H2O → C4H6O4 + CaSO4.2H2O Equation 6
To further enhance the purity of the process stream and to get rid of excess ions, a series of, i.e. cation exchangers (I-301, 303, 305, 307) to get rid of calcium ions Ion exchangers and anion exchangers (I-302, 304, 306, 308) to remove sulfate ions are employed. Two pairs of exchangers (I-301,302 & I-303,304) will remain in service for a set period of time while the other two pairs of exchangers (I-305,306 & I-307,308) will be regenerating. As the first two pairs of exchangers get exhausted, the service fluid is sent to the regenerated second pair of exchangers and the cycle gets repeated. The parallel set of exchangers are used to ensure a continuous flow through the system. The spent regenerants along with water that is used for the regeneration cycle is treated and discarded off appropriately
Section B

Section B: Succinic Acid to 1,4-Butanediol Process Flow Diagram
Hydrogenation
Downstream from succinic acid purification the succinic acid is mixed with water and recycle streams. The combined stream is then pressurized and heated before being added to the reactor. The reactor is a batch gas-liquid stirred tank reactor. The reactor is purged of oxygen using nitrogen. The catalyst is added as a powder form, and hydrogen is used to bring the vessel up to high pressure. The hydrogenation takes around 7hrs and is an exothermic reaction.
The reaction occurs by hydrogenation to gamma-butyrolactone (GBL) then to BDO, the side products tetrahydrofuran (THF), n-butanol and n-propanol are also produced at this point.
After the reaction, the liquid is removed passing through a filter to retrieve the catalyst. To ensure no hydrogen is entrained in the liquid stream a flash drum is used.
Distillation (Stage 1)
The purpose of this section of the process is to achieve the separation of the desired product, BDO, from the various other components that are formed in the hydrogenation of succinic acid in addition to the large volumes of water required to hold Succinic acid in solution at this temperature
The separation is achieved first through the use of a flash drum which removes most of the water in the product stream by separating the vapour phase water along with light ends from the liquid phase. This concentrated liquid phase is then sent to a distillation column which achieves the high levels of purity desired for the final product.
The column makes a separation designating GBL as the light key and BDO as the heavy key allowing for a very high recovery of BDO in the bottom stream along with trace levels of GBL and the highly non-volatile succinic acid. Due to the very high relative volatilities of the lighter keys the separation can be performed very effectively resulting in negligible quantities of the light ends making it into the bottoms product stream.
The distillate containing these light ends including the large quantities of water is mixed with the vapour extracted from the flash drum and is sent off as a wastewater stream which can be sent to sewerage due to the very high composition of water and the relatively undamaging nature and low composition of the other light ends.
Distillation (Stage 2)
Economic Analysis
Prices
Before the start of the project, different possibilities for final products were evaluated and the production of BDO with a market value of $3.5 per kilogram was finalised. The prices of feedstocks are compiled from several sources
CAPEX
A large part of the economics is the capital expenditure which includes the cost of all the equipment (Appendix A) within the plant (including installation-piping, instrumentation & control, electrical, civil, structures and paint) approximated to be about £22.9 million. The most expensive items of equipment being the set of batch fermenters (3) estimated to cost £4 million each. The cost of design – contractor charges are approximated as 5% of capital cost. The contingency charges including costs for inventory of raw material (2 weeks), cash on hand (1 week of production), spare parts inventory (1 week of production) were also accounted for. The total Capital investment is phased into 3 years with a split of 10%, 50% and 40% for year 1, 2 and 3 respectively. It is only after this 3 year waiting period that the final product BDO goes under production.
OPEX
Rough estimate costs for energy for overall sections were calculated. However, this may not accurately reflect reality due to deviations caused by the lack of detailed design. The need for utilities (cooling water, steam etc. were also accounted for on a yearly basis. A yearly operational cost of £1.5 million is expected. Some of the expenditure for energy can be offset by the installation of a CHP plant as initially thought of. Further reduction in costs for utilities can be seen by the treatment and recycling of waste streams like spent regenerants and water. Lastly, the cash expended for labour (skilled & unskilled), security, and maintenance are added.
Parameters
Return on Investment (ROI)

he ROI is a simple indicator for the economic performance of the chemical plant to comprehend the amount of investment is returned back to the investors per annum. ROI of about 2.97% is estimated for a span of 30 years with an initial investment of about £26.7 million.
Payback Time (PBT)
The payback time is the time required to recoup the maximum investment capital. It is the time at which the cumulative cash return gives a value of £0 (break-even point). From the cumulative cash return graph, the PBT is seen to be 17.76 years
Internal Rate of Return (IRR)
The IRR is the discount rate at which the net present value of cash flow is equal to zero. Values for different NPV at different discounting rates (1 to 16%) were found. An Internal rate of return of 5.08% was found
Sensitivity Analysis
This analysis was executed to view how well the project handles fluctuations due to external or internal factors. Certain parameters as shown in the table below were tweaked based on ‘best guess’ estimates. Final calculated values for PBT, ROI and IRR for the optimistic and pessimistic scenarios are also tabulated

Summary
Although the economic prospects for the current scenario look bleak (with the low ROI and high PBT); by introducing simple measures like treating and recycling spent utilities along with a slight increase in production, a drastic positive change in the overall economics can be observed.

Cumulative Cash Return for actual scenario (descriptive)

Sensitivity Analysis – Cumulative Cash Return for 3 scenarios

Sensitivity Analysis – Internal Rate of Return for 3 scenarios
Safety
The plant is designed with thought and consideration to a range of safety issues that may be encountered during plant start-up, operation and shut-down. The different stages of the process in this design vary greatly, presenting a wide range of safety issues. This includes high temperatures and pressures as well as dealing with high-risk components. Consequently, it is crucial that there are safety precautions in place which need to be followed strictly.
Legislation
The frequency of death toll is particularly high in chemical factories, coal mines and construction sites. The lack of safety awareness, as well as lax implementation of regulations, are contributing factors for the high rate of accidents. The government’s efforts by the State Administration of Work Safety (SAWS) has made a positive effect by reducing the number of workplace accidents due to legislation being made more stringent. Also, workplace accidents incur economic losses and reputation damage to the organisation. Hence, our process will conform to all the Chinese regulations, as listed below as well as other regulations issued by various ministries. Companies in power of producing or selling hazardous chemical need to abide by the following law:
Decree of the State Council (Decree) 591 – Safe Management of Hazardous Chemicals
It is supported by multiple ministerial guidance regulations as listed below and it is not a single law. The regulation requires businesses to apply for a license to operate hazardous chemicals.
1) Ministry of Environmental Protection (MEP) Order 7 – Environmental Management of New Substances
2) State Administration of Work Safety (SAWS) Order 53 – Administration of Registration of Hazardous Chemicals
3) Ministry of Environmental Protection (MEP) Order 22 – Environmental Administration Registration of Hazardous Chemicals
Sustainability
Three main areas of sustainability have been considered for our process:
Economic Sustainability
SCB is a reliable feedstock which will be purchased at a very low price. Before the introduction of this plant, the SCB would just have been burnt for power making the process potentially “money for nothing”. However, the process itself is costly and the economic analysis is outlined in section XX. Throughout the process where possible, recycle streams have been utilised to attempt to reduce the operating costs and emissions, reducing the utilities required for the process.
Social Sustainability
As this process is a new process development in the area of Guangxi, there will be several jobs generated for locals. This will include the likes of construction of the plant, working on the plant itself etc. Consequently, this will provide a boost to the economy of the area and the potential to increase people’s standards of living.
Environmental Sustainability
Overall, as a waste product is being used to create a product which rivals an environmentally harmful process (use of maleic anhydride) the process can be seen as environmentally sustainable. Our product is considerably more environmentally friendly than its competitors. The main issue arises with the amount of gypsum which is formed as a by-product.
The production of BDO from sugarcane bagasse is far more environmentally friendly, compared to other routes such as reacting butadiene with acetic acid. The intermediate succinic acid can also be produced from non-biological feedstocks, such as maleic anhydride. However, those approaches suffer the same environmental problem of being created from fossil fuels, specifically n-butane in the case of maleic anhydride. The primary advantage of the chosen process is the environmental benefit compared to other processes that require fossil fuels, those being far less greenhouse gases being released into the atmosphere, the damage caused to the ocean floor and land, amongst others.
For an overview of the potential threats to continued operation, see the cradle to grave diagram in appendix B. The red boxes signify processes that may be ecologically harmful, but are carried out by outside suppliers, and therefore are beyond our control.
Utilities
This section describes the uses of water and power in all the processes. The majority of the utilities needed will be taken from local sources. The following utilities will be required:
Water
Local sources will be used for water on the plant. The majority of the water will be used in the process for diluting mixtures and washing the products. Any excess water will be separated and then discharged into a cooling channel. Here the heat will be able to dissipate before rejoining the surrounding water sources.
Bactria and Nutrients
Bacteria and Nutrients are used in the fermentation process. Nutrients are acquired from Sigma Aldrich while the bacterium is from German Collection of Microorganism and Cell culture.
Steam
Steam will be produced on site for the use in the steam explosion reactor, heat exchangers and reactor steam jackets. The water used in the steam production will be chemically purified from a local water supply.
Power
The largest part of the power consumption required will be for the operation of pumps and compressors. Power will also be vital for the use of process control systems.
Waste and Effluent Treatment
The production of succinic acid and BDO will produce multiple waste streams which may require treatment. Organic waste consisting of biomass, nutrients, water from the bio-succinic acid purification stage, will need to be sent to a wastewater treatment plant (WWTP). Also needing to be disposed offsite in this stage will be gypsum. As impurities are present, gypsum that is formed will not be suitable for reuse by another industry due to a yellowish colouration and unpleasant odour. Hence, it is sent to landfills as waste.
Carbon dioxide
It will be used in the fermentation stage for conversion to succinic acid. It is sent downstream of the fermentation after which most of it is recycled back to the fermenter while some if it is purged to the atmosphere.
Decommissioning
Quality Control / Quality Assurance
A good QC/QA Plan is essential to ensure the design intent is met and all processes operate as required. The plan would commence during the detailed design, through procurement and right through construction and hand over to operations.
Commissioning and Testing
This is an important stage of any project and if executed properly will ensure the plant is started up safely and efficiently. Normally divided into the various disciplines, for example – mechanical, electrical and control & instrumentation. A typical commissioning plan for mechanical would require the testing of all valves and pumps to ensure they are installed correctly and the right orientation. For safety and environmental reasons, a low-pressure air test would be carried out looking for any leaks. Upon successful completion of the air test, a water pressure test would be carried out. This would all be tested and commissioned prior to the introduction of any ‘live’ products. A large amount of electrical equipment is safety related and must be commissioned and tested before start-up. This would involve going through the P&ID line by line to ensure the electrical equipment has been installed correctly and functions as designed.
Start-up
Following the installation of all equipment, control systems and infrastructure several tests need to be undertaken to ensure the plant is in safe operating order. All pipework (valves, welding, connections etc.) will be thoroughly checked and will have to be passed fit for operations. These tests will include pressure and temperature checks to ensure no leaks or blockages. Each unit needs to undergo hydrostatic testing. A strength test is carried out to ensure a pressure loss of no more than 2% an hour is exceeded. Following this test, welds and joints should be inspected to look for wet spots – indicating leaks in the unit. Control systems need to be checked to be operating correctly. All wiring and connections need to be correctly set up and done so in a safe operating manner. All corresponding software needs to be working correctly. When a start-up is necessary following any shutdown, water will be passed through to ensure removal of any solids and clean the system.
Shut-down
Several scenarios are possible which include the entire plant or individual units being shut down for scheduled maintenance, cleaning or an emergency. The entire system will be shut down by stopping the addition of feedstock and closing of valves which feed the reactor [R101]. This will, in turn, cause the shutdown of the following sections. Under a planned shutdown procedure, the process would run through, processing the feedstock, shutting off each area of the plant as the production proceeds. If this occurs, once the system has been cleared, all valves will be opened to ensure gas flow out of the system. There are no hazardous gases present in the plant
Conclusions and Recommendation
While the process is effective in achieving its aims of sustainably producing a valuable product in BDO from agricultural waste, there are still improvements that can be made to the process.
The use of water in the process is not particularly sustainable or cost effective. For the succinic acid to be held in the liquid phase even at elevated temperatures, large quantities of water are required which vastly exceed the total composition of all the other reaction products. This issue is exacerbated by the fact the process in its current design lacks a way of recycling this water. This leads to large quantities being sent to waste water treatment plants putting a strain on natural resources and hurting the plant sustainability. This problem could be alleviated by introducing a recycle stream for the used water along with a purge stream to prevent the buildup of side products in the process. While this would not completely remove the need for water, it would significantly reduce the quantities required. It is estimated that purging as little as 20% of the water could still allow for a product of 99% purity with substantial economic and environmental benefits.
Another concern is the cost-effectiveness of the process. The economic analysis shows that the payback time is relatively high. In an attempt to reduce this, the production rate could be increased as by doing so, the profits that would follow would substantially increase. This would make the process far more financially viable and hence reliable and attractive to investors while also reducing the risks involved by greatly shortening the time required to pay off the initial investment.
In order to achieve the production increases, in addition to the necessary larger scale equipment, more resources will be required including larger quantities of feedstock. It has been suggested that a potential method of resolving this issue could be to diversify the feedstock. There is the potential to adapt the process to deal with different agricultural waste biomass products from other industries and processes such as cornstalk and food waste. These alternative feedstocks could potentially be used alongside the sugarcane bagasse or even be combined to form a composite feedstock. Making such adaptions would not only increase the maximum production capacity of the process but would also increase the economic reliability and viability of the process.